If you’re managing a corrugated manufacturing facility, you know the challenges of manual dunnage placement. The TopBot system, developed by 20/20 Robotics, transforms this labor-intensive task into an automated process, saving time and protecting your workers. This guide shows you how to bring TopBot’s automation advantages to your facility.
Understanding TopBot’s Capabilities
Your manufacturing line faces constant pressure to increase output while maintaining quality. TopBot addresses these demands by combining robotics with 2D & 3D vision systems to place dunnage – protective material on top of corrugated sheet stacks – with machine precision.
The system handles more than 200 units hourly with cycle times as brief as 15 seconds, matching your high-speed strapping equipment without creating bottlenecks. In a 50,000-square-foot facility, TopBot typically requires only 550 (400 if you don’t count the conveyor belt that we are placing on) square feet of floor space while replacing manual handling operations.
The precision placement improves product appearance and stability during shipping. You’ll see reduced workplace injuries from manual handling in conveyor zones while cutting labor costs.
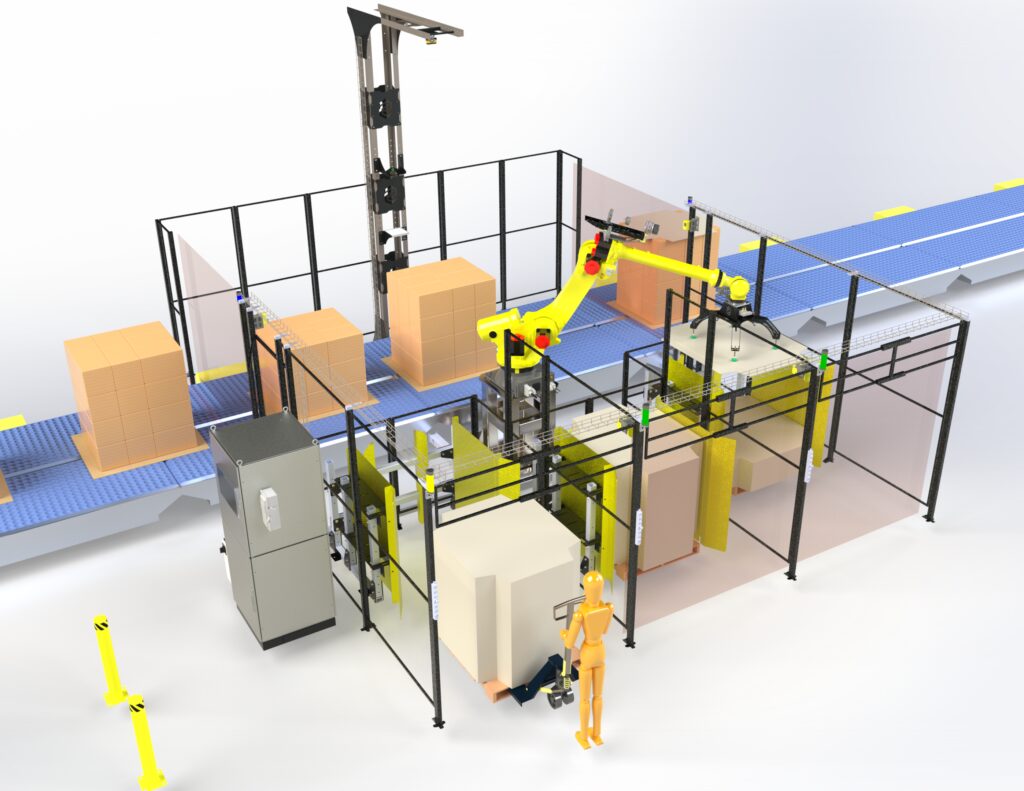
Implementation Process
Step 1: Initial Assessment
Before installation begins, we’ll evaluate your production environment to create your custom implementation plan. We’ll analyze your conveyor systems, map out integration points, and design a strategy that keeps your current operations running smoothly during the transition.
Step 2: Facility Preparation
Your facility needs the right foundation for TopBot to perform at its best. Our team will help you establish proper power infrastructure (480V 3-phase power), install safety systems, and modify conveyors as needed. We’ll install emergency stops, mark clear operation zones, and verify all utilities meet system requirements.
Step 3: Installation and Integration
Your technical implementation begins with precise positioning of the robotic system. We’ll establish control connections and integrate TopBot with your equipment. Testing validates communication between TopBot and your line PLC to confirm smooth operation with your production processes.
Step 4: System Configuration
Your TopBot system needs precise calibration to match your production requirements. We’ll program it to recognize your specific stack configurations, set optimal dunnage placement patterns, and establish quality parameters that maintain consistency across all your product specifications.
Step 5: Staff Training
Your team’s success with TopBot starts with proper training. We’ll teach your operators the daily procedures, safety protocols, and basic maintenance tasks. Your staff will master performance monitoring, troubleshooting, and quality checks through hands-on practice with the system.
Step 6: Testing and Optimization
Before full production begins, we put your TopBot through rigorous testing. We verify accuracy, optimize cycle times, and fine-tune vision systems to your specific needs. This confirms your system meets all performance metrics and safety requirements.
Best Practices for Long-term Success
To maximize your investment in TopBot automation, following proper maintenance and operation procedures is essential. Regular calibration keeps your system precise and reliable, while scheduled vision system cleaning prevents quality issues. Document your procedures to maintain consistency as you train new operators.
Track key metrics like cycle times, accuracy rates, and maintenance patterns to spot optimization opportunities. Schedule regular team meetings to review performance data and address operational questions, helping you get the most from your automation investment.
Ready to transform your dunnage placement operations with TopBot? Visit our Dunnage TopBot Solutions page to learn about implementing this automation solution in your facility.
Frequently Asked Questions
What is the average installation time for TopBot?
Installation typically takes 3-5 days, depending on facility preparation and integration requirements.
How does TopBot handle different stack sizes?
The 3D vision system automatically detects and adapts to varying stack dimensions and configurations, requiring minimal manual adjustment.
What maintenance does TopBot require?
Regular maintenance includes vision system cleaning, calibration checks, and standard robotic maintenance procedures, usually performed weekly or monthly based on usage.
Can TopBot integrate with existing conveyor systems?
Yes, TopBot is designed to integrate seamlessly with standard corrugator conveyor systems and strapping equipment.
What safety features are included?
TopBot includes emergency stops, safety barriers, and automated shutdown protocols to protect workers and equipment.